Trying to decide between PA6 and PA66 for your next engineering application? You're not alone. These two nylon materials—PA6 (Polyamide 6) and PA66 (Polyamide 66)—are among the most commonly used engineering plastics in industries like automotive, electronics, and consumer goods. While they appear similar at first glance, their mechanical strength, thermal resistance, and moisture absorption properties differ in critical ways.
At All Around Compounding Co., Ltd. (All Around Polymer Co., Ltd.), we specialize in customized nylon compounds designed for performance and reliability. In this guide, we provide a detailed PA6 vs PA66 comparison—including key differences, material properties, pros and cons, and the best use cases—so you can make informed material choices backed by expert insight.
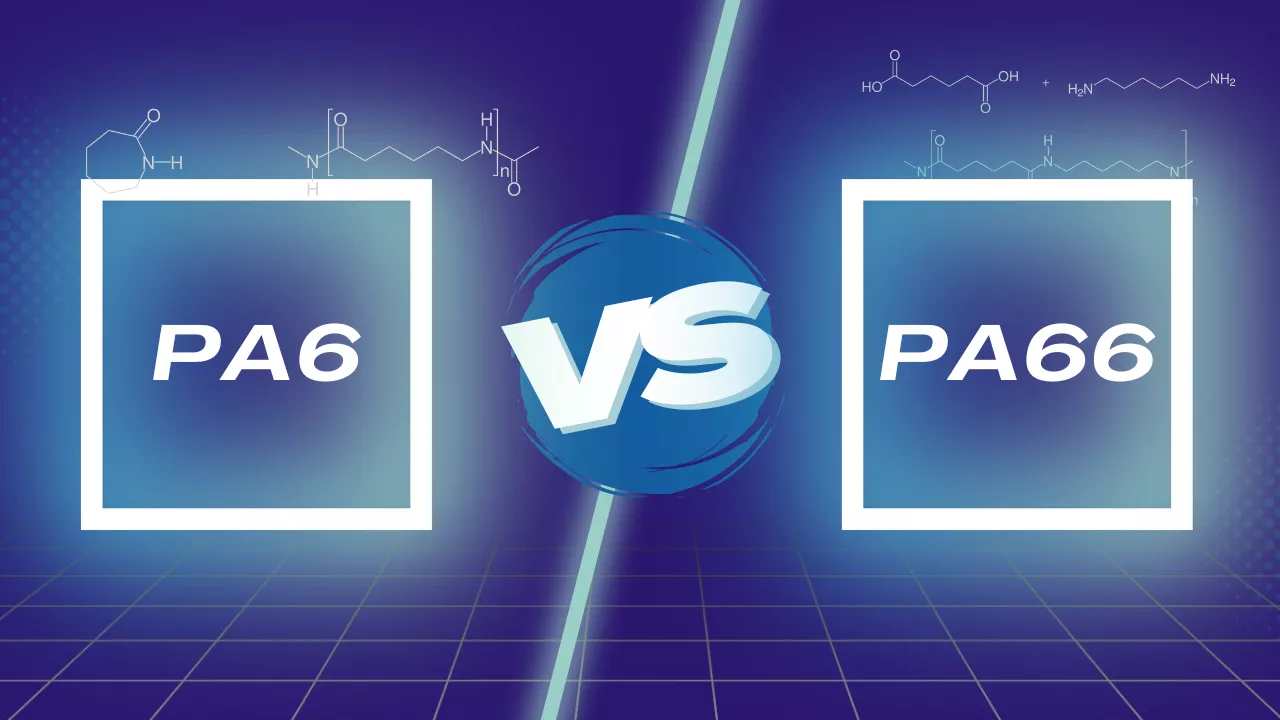
Understanding the Differences Between PA6 and PA66
Both PA6 and PA66 are semi-crystalline nylons with excellent mechanical and thermal properties. However, their structural differences lead to distinct performance profiles.
PA6 vs PA66 : Visual Performance Comparison
To help you quickly grasp the strengths of each material, the chart below provides a side-by-side visual comparison of PA6 and PA66 across seven key performance dimensions, including tensile strength, thermal resistance, cost, and ease of processing.
Properties |
PA6 |
PA66 |
Molecular Structure | Single repeating unit | Two repeating units |
Density (g/cm³) | 1.13 | 1.14 |
Melting Point (°C) | 220 | 260 |
Water Absorption | Higher | Lower |
Crystallinity | Lower | Higher |
Tensile Strength (MPa) | Lower | Higher |
Impact Resistance (kJ/m²) | Higher | Lower |
Thermal Stability (°C) | Continuous use up to 180°C | Continuous use up to 200°C |
Processing Temperature (°C) | 230 - 250 | 270 - 290 |
Molding Temperature (°C) | 80 - 100 | 90 - 120 |
Molding Shrinkage (%) | 0.6 | 0.8 |
Heat Deflection Temperature (°C) | 170 | 250 |
Applications | Automotive parts, Office furniture, Bicycles | High-stress automotive parts, Electrical components, Sports equipments |
Chemical Structure of PA6 and PA66
- PA6 is synthesized via ring-opening polymerization of caprolactam.
- PA66 is made through polycondensation of hexamethylenediamine and adipic acid (6 carbon atoms each).
These small differences result in distinct property variations, especially in moisture absorption, thermal stability, and mechanical performance.
📖 Recommended Reads for Material Engineers:
📌 Engineering Plastics: Common Types and Applications
Understand where PA6 and PA66 fit among other popular engineering plastics.
📌 Top Plastics for Metal Replacement in Manufacturing
Explore why glass-filled PA66 is a top choice in replacing metal components in high-stress applications.
Advantages and Disadvantages of Each Material
PA6 Advantages:
- Easier to process due to lower melting point
- Higher impact resistance and flexibility
- More cost-effective for general-purpose applications
PA6 Limitations:
- Higher water absorption can lead to warpage
- Lower strength and stiffness compared to PA66
PA66 Advantages:
- Superior tensile strength and rigidity
- Excellent heat resistance for high-temperature environments
- Lower moisture absorption for better dimensional stability
PA66 Limitations:
- Requires higher processing temperature
- Higher cost compared to PA6
Application-Based Comparison : Which Nylon Fits Your Needs?
Application Type | Recommended Nylon | Reason |
Flexible automotive parts | PA6 | Better impact absorption and easier molding |
High-temperature engine components | PA66 | Greater thermal stability and load resistance |
Electrical connectors and switches | PA66 | Flame retardancy and dimensional reliability |
Office furniture and structural plastic | PA6 | Cost-effective with sufficient toughness |
Sports equipment (e.g. helmets, bindings) | PA66 | High mechanical strength and rigidity |
Bicycle components | PA6 | Good flexibility and shock resistance |
Enhancing Performance Through Compounding
For more demanding requirements, PA6 and PA66 can be modified or reinforced with various fillers to enhance their original properties and expand their range of applications. These modified or reinforced nylons are referred to as nylon compounds. Reinforcing PA6 and PA66 with fillers like glass fiber, carbon fiber, or impact modifiers can improve their properties:
-
Increased Strength and Stiffness: Reinforcing PA6 and PA66 with glass or carbon fibers results in composites that can handle higher loads and stress without deforming. (Read more: Top Plastics for Metal Replacement in Manufacturing : Benefits, Choices, and Analysis)
-
Enhanced Thermal Properties: By adding specific fillers, the heat resistance of these nylons can be improved, allowing them to maintain performance at elevated temperatures. (Read more: How to Select Car Headlight Housing Materials)
-
Improved Dimensional Stability: Reduced water absorption and enhanced rigidity help maintain the shape and size of components, even in variable environmental conditions.
-
Improved Toughness: Impact modifiers can significantly improve the toughness of nylon composites, making them ideal for applications where durability and resistance to sudden forces are critical. These modifiers help absorb and dissipate energy, reducing the risk of material failure under impact. (Read more: Enhance Nylon Durability and Flexibility with the Right Impact Modifier)
Composite Type | Enhancements |
Glass Fiber Reinforced | Enhances strength, stiffness, and dimensional stability. Used in automotive components, power tools, and sports equipment. |
Mineral-Filled | Improves rigidity and thermal stability. Commonly used in electrical housings and structural parts. |
Flame-Retardant | Provides safety in electrical and electronic applications, used in connectors and switches. |
Carbon Fiber Reinforced | Offers excellent strength-to-weight ratio and electrical conductivity. Used in aerospace, automotive, and high-performance sports equipment. |
Impact Modified | Increases toughness and resistance to impact forces, reducing fracture risks. Suitable for applications requiring enhanced durability and shock absorption. |

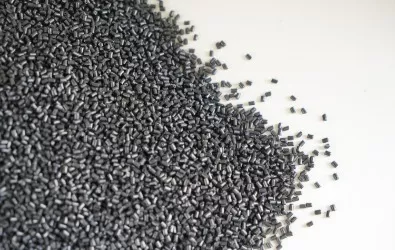
Common Applications of PA6 and PA66
PA6 and PA66 are widely used in various industries due to their unique properties. Here's a look at some common applications:
PA6 Applications
-
Automotive Industry: PA6 is used in the production of flexible parts such as steering column, seat belt buckle, and side mirror assembly due to its good impact resistance and moderate tensile strength.
-
Office Furniture: PA6 is utilized in manufacturing various office furniture components, offering good flexibility and durability.
-
Bicycles: PA6 is employed in the production of bicycle parts, providing necessary flexibility and impact resistance for different components.
PA66 Applications
-
High-Stress Automotive Parts: PA66 is preferred for high-stress parts such as engine components, manifold, fuel rail and water tank cover owing to its superior tensile strength and higher thermal stability.
-
Electrical Components: PA66 is used in connectors, switches, and other high-performance electrical components where rigidity and dimensional stability are crucial.
-
Sports Equipment: PA66 is ideal for applications requiring high mechanical strength and rigidity. It is commonly used in the production of ski bindings, helmets, and protective gear, providing durability and safety in demanding sports environments.
Recycling Challenges of PA6 and PA66
Although both PA6 and PA66 are technically recyclable, their similar appearance and processing behavior often make it difficult to separate them during mechanical recycling. When mixed, the resulting material may suffer from degraded thermal and mechanical properties, making it unsuitable for applications that demand specific performance standards.
Technologies like NIR (Near-Infrared) spectroscopy are becoming valuable tools in distinguishing PA6 from PA66—especially in improving sorting accuracy during recycling. By analyzing the material-specific absorption patterns of near-infrared light, these systems can assist in enhancing the purity of recycled output and reducing cross-contamination risks.
FAQ: Frequently Asked Questions About PA6 and PA66
-
Which nylon type is better for high-temperature environments? PA66, due to its higher melting point and thermal stability.
-
What are the cost considerations between PA6 and PA66? PA6 is generally more cost-effective, while PA66 offers superior strength and rigidity at a higher cost.
-
Can PA6 and PA66 be recycled? Yes, both are recyclable, making them environmentally friendly options.
Case Study : Engine Component Optimization with PA66
Client : A global Tier-1 automotive supplier
Challenge : Required a material for high-temperature engine components subject to vibration and load
Our Solution : We recommended a glass fiber-reinforced PA66 composite. This provided:
- Excellent dimensional stability under heat cycling
- Superior tensile strength for structural loads
- Reduced moisture-related warpage in humid conditions
Outcome : The client successfully introduced a new engine part series with improved performance and reliability, while reducing the failure rate by over 30%.
Final Thoughts : Make the Right Nylon Choice
Selection Criteria | Choose PA6 | Choose PA66 |
Budget-friendly applications | ✅ | |
High heat resistance | ✅ | |
Dimensional accuracy under humidity | ✅ | |
Shock and impact resistance | ✅ | |
Ease of molding and fast cycle times | ✅ | |
Long-term structural stability | ✅ |
Both PA6 and PA66 offer substantial benefits, but their performance profiles vary depending on processing demands and application needs. PA6 is an excellent choice for general-purpose, impact-resistant applications, while PA66 is preferred in high-stress and high-temperature environments.
Moreover, reinforcing PA6 and PA66 with materials like glass fiber, impact modifiers or carbon fibers can significantly enhance their mechanical properties, allowing them to achieve better performance in demanding applications. This reinforcement enables these nylons to handle greater stress and environmental challenges, making them more versatile and reliable for various industrial uses.
Contact the Nylon Composite Experts for Your Material Needs
At All Around Compounding, we specialize in developing tailored nylon solutions—whether you're aiming for lightweight design, improved thermal resistance, or enhanced durability. Our technical team can help you evaluate your options and provide compound recommendations specific to your product requirements.
📩 Need a quote or material recommendation?
Contact us at info@aaccl.com for expert advice and high-quality nylon composite solutions tailored to your needs.